Comprehensive Overview: What is Porosity in Welding and How to Prevent It
Wiki Article
Comprehending Porosity in Welding: Exploring Reasons, Effects, and Prevention Methods
Porosity in welding is a persistent obstacle that can significantly influence the quality and honesty of welds. As specialists in the welding industry are aware, recognizing the reasons, results, and avoidance methods associated with porosity is vital for accomplishing robust and reliable welds. By diving into the source of porosity, examining its destructive impacts on weld quality, and checking out effective avoidance methods, welders can enhance their expertise and skills to generate top notch welds regularly. The intricate interaction of factors adding to porosity requires a thorough understanding and a positive strategy to make sure effective welding results.Typical Reasons of Porosity
Contamination, in the kind of dirt, oil, or rust on the welding surface area, develops gas pockets when heated up, leading to porosity in the weld. Improper protecting takes place when the protecting gas, generally utilized in procedures like MIG and TIG welding, is unable to completely shield the molten weld swimming pool from reacting with the surrounding air, resulting in gas entrapment and succeeding porosity. Additionally, insufficient gas coverage, typically due to inaccurate circulation rates or nozzle positioning, can leave parts of the weld unprotected, allowing porosity to develop.Results on Weld Quality
The presence of porosity in a weld can significantly compromise the overall quality and integrity of the bonded joint. Porosity within a weld develops gaps or dental caries that deteriorate the framework, making it much more vulnerable to breaking, corrosion, and mechanical failing.In addition, porosity can prevent the efficiency of non-destructive testing (NDT) techniques, making it testing to identify various other problems or gaps within the weld. This can result in significant safety and security worries, particularly in crucial applications where the structural honesty of the welded components is paramount.

Prevention Techniques Review
Provided the destructive impact of porosity on weld high quality, effective prevention techniques are essential to maintaining the architectural stability of welded joints. In addition, picking the proper welding parameters, such as voltage, existing, and travel rate, can assist reduce the threat of porosity formation. By incorporating these avoidance techniques right into welding methods, the event of porosity can be dramatically decreased, leading to more powerful and much more dependable bonded joints.Significance of Correct Shielding
Correct shielding in welding plays a crucial duty in avoiding atmospheric contamination and making certain the integrity of bonded joints. Shielding gases, such as argon, helium, or a blend of both, are commonly utilized to shield the weld pool from responding with components in the air like oxygen and nitrogen. When these reactive components enter into contact with the warm weld swimming pool, they can cause porosity, causing weak welds with minimized mechanical homes.
Inadequate shielding can cause various problems like porosity, spatter, and oxidation, jeopardizing the structural stability of the welded joint. For that reason, sticking to proper shielding techniques is vital to generate high-quality welds with marginal issues and make sure the durability and integrity of the bonded elements (What is Porosity).
Surveillance and Control Techniques
Exactly how can welders effectively keep an eye on and regulate the welding process to ensure ideal outcomes his response and protect against problems like porosity? By constantly monitoring these variables, welders can identify variances from the excellent conditions and make instant changes to stop porosity formation.
Furthermore, carrying out correct training programs for welders is essential for keeping track of and managing the welding process successfully. What is Porosity. Informing welders on the relevance of keeping regular criteria, such as correct gas securing and take a trip rate, can aid protect against porosity concerns. Normal analyses and qualifications can additionally make sure that welders excel in monitoring and controlling welding procedures
In addition, making use of automated welding systems can improve tracking and control abilities. These systems can precisely manage welding criteria, minimizing the probability of human error and guaranteeing regular weld high quality. By integrating advanced surveillance modern technologies, training programs, and automated systems, welders can successfully keep track of and control the welding procedure to lessen porosity problems and attain high-grade welds.
Final Thought
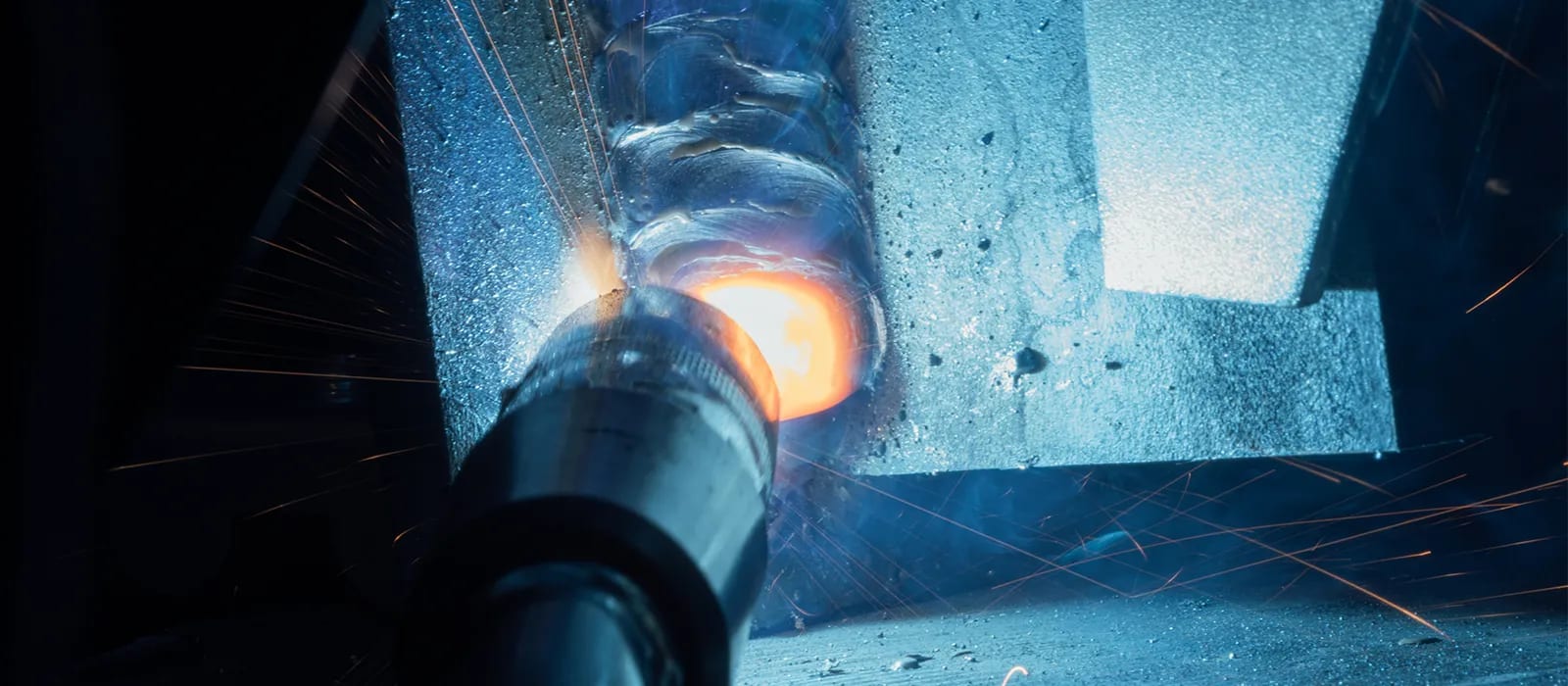
Report this wiki page